Behind the scenes at Majuno

Naturally, it's in Auvergne, the home to French volcanoes, that Jean-Charles Matrone works with lava stone in his workshop. He has transformed a timeless stone into an exceptional contemporary piece, fruit of his burning imagination.
Tradition Pierre is the name of the workshop run by Jean-Charles Matrone and his wife Anne-Sophie. It is located in Lempdes, in the Puy-de-Dôme region, at the foot of the Auvergne volcanoes. It's from these hills that Jean-Charles obtains the raw material for his work : the lava stone. More precisely, he works with Volvic stone, sourced from quarries in the region.
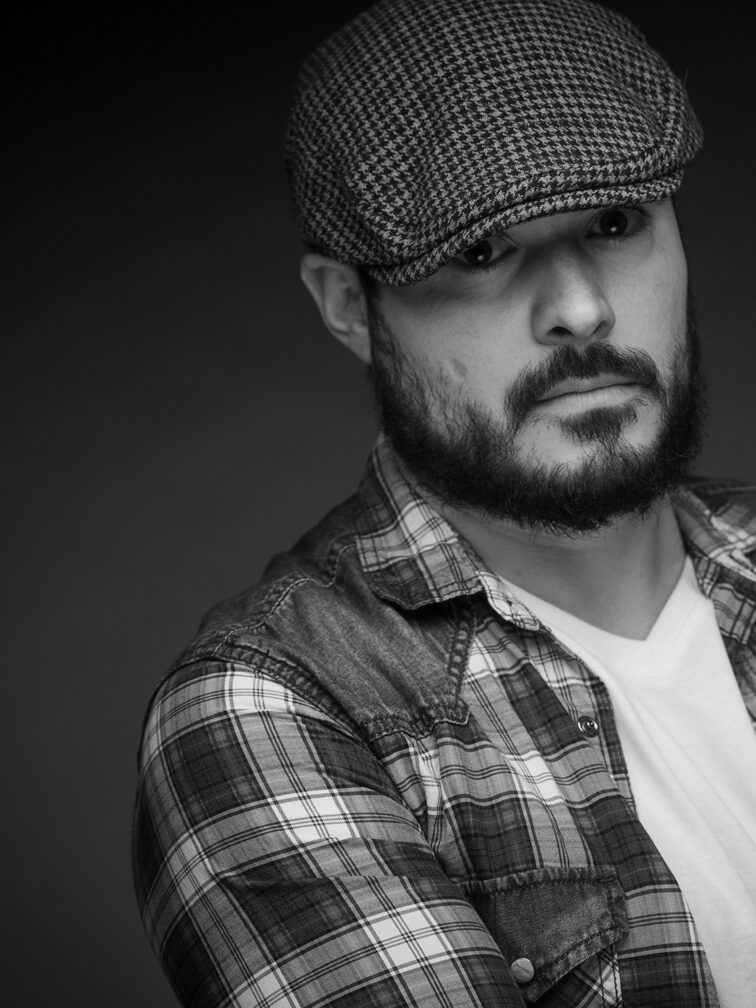
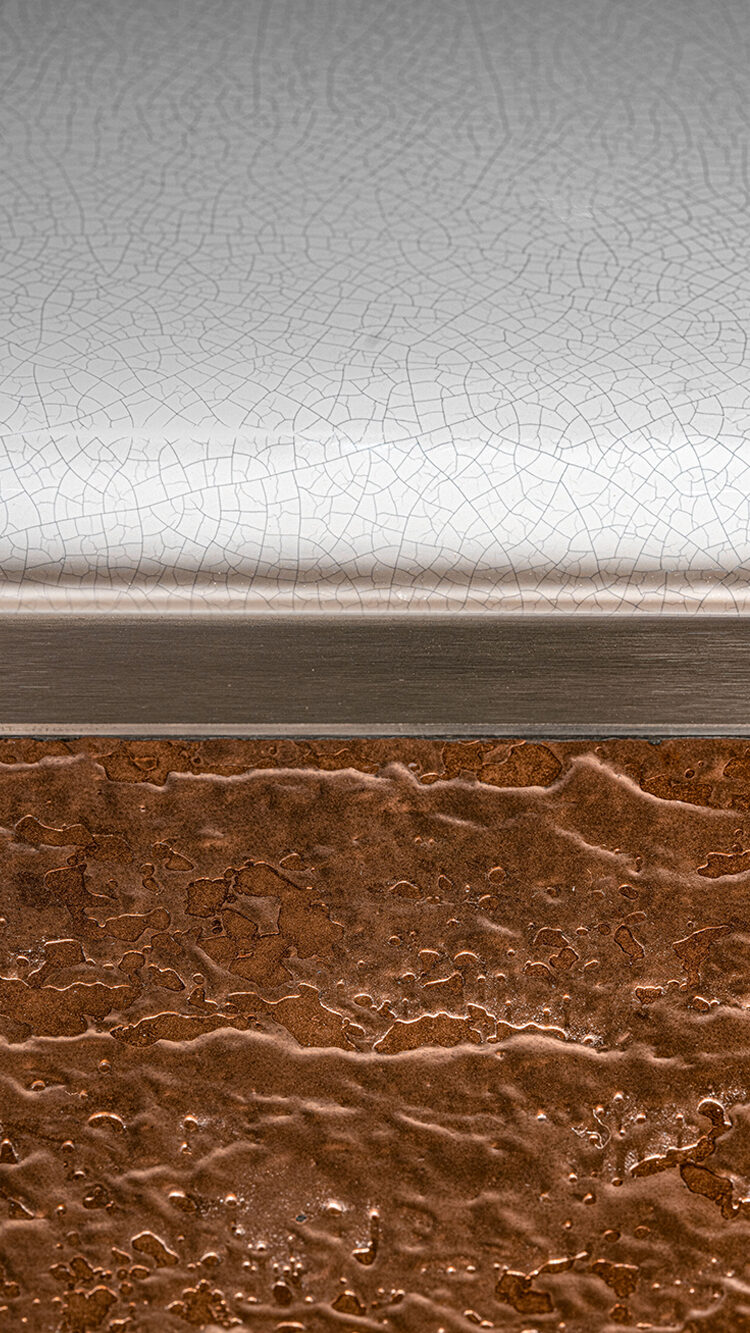
Why did you choose to work with lava stone ?
My father, Aimé, was a contractor. He did masonry and painting, and I often went with him to construction sites and quarries. After observing him work and helping him out, I decided to learn stone-cutting. Then I did my training in a lava enameling workshop in Auvergne.
Over time, my wife and I decided to open our workshop in order to create our own designs. We're very happy with the way things went, as we now have the chance to work with some phenomenal decorators and designers. I'm very proud of this French expertise, which is becoming increasingly international.
Starting with a thousand-year-old stone, and thanks to our know-how, we design and manufacture all kinds of furniture pieces for private customers or emblematic landmarks. We were asked, for example, to completely redo the façade of La Samaritaine as part of the renovation work. The volcanoes of Auvergne, allied to this symbol of Parisian life... do you realise? I like the idea of restoring the reputation of this long-forgotten material and taking it all the way to the greatest architects' offices.
How does one go from raw lava stone to the piece that you created for Majuno ?
I work closely with the quarries in the Auvergne region where I source my materials. But that is just the beginning of a long process. The stone then needs to be washed, dusted and cleared of any imperfections. It is then fired for the first time before being left to cool and dry for around twelve hours. We then apply what we call clay slip, a coating that smoothes the stone by filling in the pores in the lava. Then we fire it at 960 degrees.
After that, it's time for Alain, our enameller, to enter the scene. He has specifically created these colors for the table. The saffron, grey and black hues come from his blends of Limoges enamels. Once the enamel has been sprayed on, the piece is returned to the oven for eight hours. Behind its somewhat rugged appearance, lava stone requires a great deal of care, patience and attention to achieve its full potential.
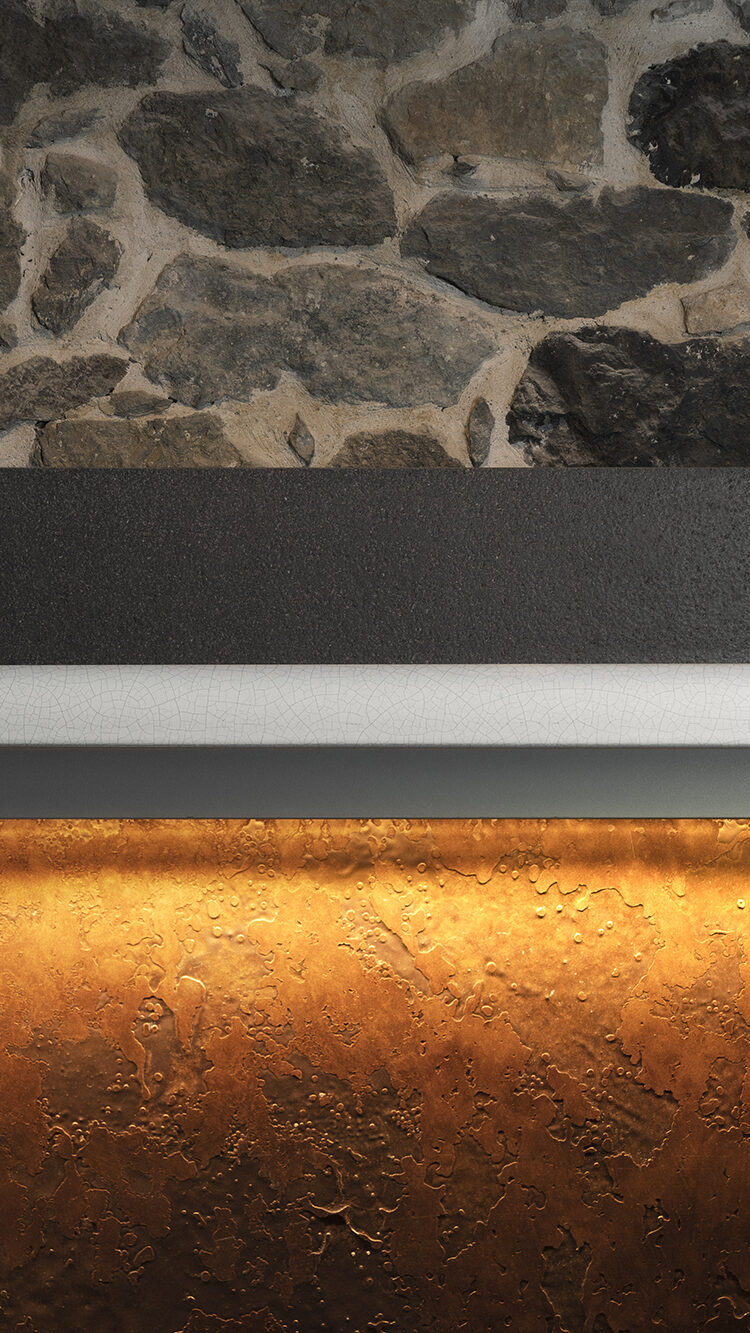
You seem to love this material more than anything else...
Yes, it's true. I also like the idea of embellishing a natural material that's a bit rough to start with. Lava stone has nothing but advantages : it's very resistant, and it doesn't scratch or get stained. How can you not love it ?
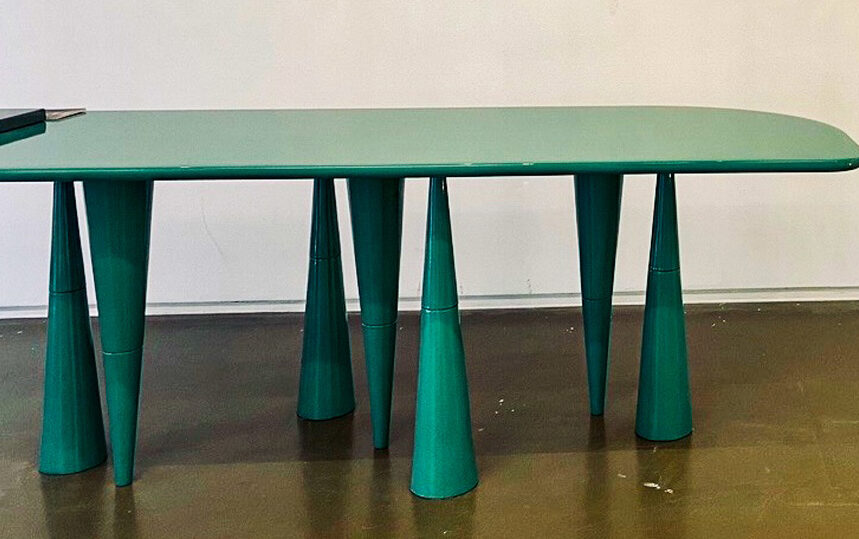